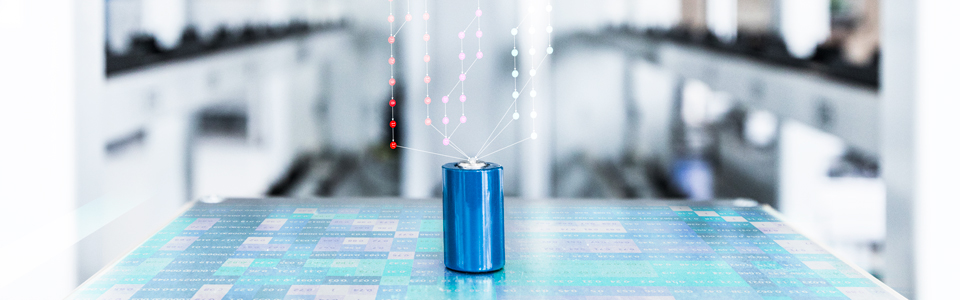
Digitalization is of crucial importance for improving the efficiency, sustainability, and scalability of battery cell manufacturing. The process can be methodically divided into three progressive levels: Transparency, Aggregation, and Autonomy. Each of these levels plays a decisive role in transforming traditional manufacturing into a modern digital enterprise.
The evolution from basic transparency to full autonomy not only enhances the operational efficiency of battery manufacturing but also supports the industry's endeavor for more sustainable and economically viable production practices. Thus, digitalization is not merely an operational upgrade but a strategic necessity in the modern energy landscape, essential for maintaining a competitive edge and meeting the growing global demand for battery technology. By systematically investing in these levels of digitalization, manufacturers can transform their production lines into the intelligent factories of the future, optimizing resources and maximizing output with the highest precision.
The foundation of digitalization begins with achieving transparency in the manufacturing process. This is primarily achieved through the use of sensors and automated data collection systems that capture and transmit real-time operational data. These raw data are then visualized on simple dashboards, providing immediate insights into production metrics. The initial investments at this level are substantial, as they require extensive hardware integration. However, the scalability achieved through additional hardware installation is a critical step. Despite the high initial costs, this level does not produce direct added value due to the lack of feedback mechanisms. It serves as the essential groundwork for more advanced digitalization efforts.
At this intermediate level, complexity management is facilitated by digital technologies such as simulation tools and applications like Statistical Process Control (SPC) and alarm systems that are triggered when set thresholds are exceeded. This stage involves moderate investment costs and scales through the integration of additional Information Technology (IT) and Operational Technology (OT) systems. Data aggregation provides new levels of information, creating modest added value through enhanced situational awareness and preliminary analytical capabilities. This enables manufacturers to not only monitor but also predict and adjust processes with greater accuracy.
The culmination of digitalization in battery cell manufacturing is autonomy. This level leverages the infrastructure and data insights from the previous levels to implement automated actions and feedback loops directly into the production process. This automation includes advanced control systems and decision-making algorithms that operate independently to optimize manufacturing outcomes. The investments required remain moderate, but the scalability and value generated are significantly higher due to the incorporation of sophisticated know-how. Autonomous systems enable rapid and robust responses to production variables, enhancing process efficiency and product quality through continuous improvements and innovations, both directly and indirectly.